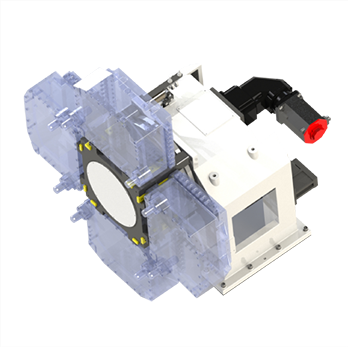
AHC
Each Cubic is equipped standard with AHC(Automatic Head Changer), which allows Cubic to switch its heads at high speed automatically according to the process.
Cubic is cutting edge hole processing machine which provides excellent flexibility and versatility. Its ability of combining processes and reducing the required amount of traditional machines helps to make huge cost savings. Cubic can not only make manpower saving possible but also achieve high quality products.
By replacing from 3 to 6 NC equipment with one Cubic, up to 80% production space can be saved. SAKURAI offers the best produciton line planning and optimization.
One Cubic can replace from 3 to 6 traditional NC equipment, that helps to conserve energy and protects environment.
Cubic can effectively reduce the number of attachment device or eliminate transportation waste. For example, over 80% of hydraulic tank, toolant tank, robots and gantry loader can be cut.
Reduction on the number of line machines helps to decrease monthly and yearly maintenance activities. Cubic provides great reliability with easy to maintain features.
Reduction on line machines leads to reduction on the number of machine operators, that not only helps to sovle manpower shortage but also save labor costs. The number of robots can be also reduced.
Compared with machining center line type, through process integration of Cubic, line layout can be optimized, that allows manufacturers to save over 50% of factory floor space, therefore, efficient floor space ultilization can be achieved.
When investing a new production line, Cubic helps to reduce initial investment costs and maximize production efficiency right from the start. Cubic can also contribute to labor saving, efficient space ultilization and energy reservation.(63% factory floor space and 66% energy can be saved.) 〈SAKURAI data〉
SAKURAI oversees all aspects of production through its one-stop turnkey solution. One-stop turnkey solution and our solid teamwork allow us to achieve high-quality production, reliable quality management and quick delivery.
According to evolving needs in various fields, our ability to develop cutting-edge technology brings products with high added value to the world market. Customer satisfaction is always our first priority.
We has obtained very satisfying results in processing cylinder block, cylinder head, and transmission case. Our machine tools are the result of the synergy of innovative craftsmanship skills and cutting-edge technologies.
We demonstrate our ability to develop machine tools with great flexibility and offer high value added products and services to motorcycle industry across the world, which has brought SAKURAI an excellent reputation in the world market.
We not only supply parts to construction industry but also design and develop machine tools for construction equipment according to complex production process or special parts specifications. We have achieved excellent result in developing machine tools with originality, rigidity and durability.
Our ability to develop from single machine tool to special-purpose production line system gives us the possibility to take a world with a wide range of products that include outboard motor parts, agricultural machinery parts and so on.
Our machine tools and lines are flexible enough to handle different production in various fields such as automotive and industrial machinery. SAKURAI offers the most appropriate method.
※Our original 3D model
※Our original 3D model
※Our original 3D model
※Our original 3D model
※Our original 3D model
※Our original 3D model
※Our original 3D model
Over 30 years of proven track record, standard Cubic has showed reliability. Our ability to develop cutting-edge technology continues to bring products with high added value. Cubic will keep evolving with the times.
3WAY can be considered as FMC which consists of three units of Cubic. Three advanced head changers are of T-like allocation around automatic pallet changer on which three index tables are installed, therefore, two sided machining can be completed in one chucking. 3WAY has the machining capacity which is equivalent to about 12 units of conventional MC. In addition, it can also help to eliminate transportation waste on the factory floor.
Transfer line can be a combination of several units of Cubic sequential arranged, that efficiently combine processes and reduce required number of conventional machines. It can sometimes replace half of conventional machining center on a mass production line. By combining processes such as machining and measuring, transfer line can increase productivity and improve precision. Transfer line can be also developed by making use of both Cubic and machining center.
Cubic series has won international recognition and will continue to evolve with the times.
It has been 30 years since the first model of Cubic was developed. To respond to the needs of high speed and compact size, various options are provided. SAKURAI continues to meet expectations of customers.
Each Cubic is equipped standard with AHC(Automatic Head Changer), which allows Cubic to switch its heads at high speed automatically according to the process.
"Swarf to Swarf" time is only 4.5 seconds, although each head is weighting in about 300kg with tooling. The head switching speed has been 2.5 times faster than the first model and it will continue to be improved.
Cubic has the option to be equipped with 6 or 7 heads through AHC on the top of the machine which can be also used as AHS(Automatic Head Stocker), therefore, AHS not only helps to accommodate various workpiece models but also brings production flexibility.
Our original multi-spindle heads are the result of cutting edge technology and innovative craftmanship, that gaurrantees high quality prodution and accuracy. We have a track record of mounting 50 spindles into one head.
Our high speed spindle enhances high-speed, rigidity and accuracy to finally reduce machining time and down time. The spindle speed is up to 12,000rpm(1,600rpm for tapping). We make the most of our originality.
The body of Cubic is standardized with design of great originality. Over 30 years of proven track record, it has showed reliability.
While having incredible machining capability, Cubic achieves a compact body, that helps to save factory floor space. (The body size is almost equivalent to #40 machining center)
Machine bed is designed to be easily removed partly on both sides, therefore, it is easy to arrange Cubic to customers' line layout or line concept. After produciton of one workpiece model ends, Cubic can be easily arranged to another mass production line.
It is convenient to equip Cubic with devices and the IoT can connect those devices equipped with identification, communication and processing capabilities. The IoT intelligent systems enable remote control and rapid response to manufacturing detects.
Although Cubic owns greater processing capability than conventional machining center, its energy consumption is almost same as #40 machining center or even less. Cubic is eco-friendly equipment which reduces running cost for manufacturers in long term.
Model |
Cubic 4&6 | SpeedMagic |
---|---|---|
Control | FANUC35i-MB | |
Axis control | 1axis | |
Max stroke | 500mm | |
Workpiece size | 500mm×450mm | |
Spindle motor | Max 15Kw | Max 37Kw |
Rotation speed | Max 3,500rpm | Max 12,000rpm |
Head to Head | 2.0sec | 1.0sec |
Swarf to Swarf | 7.5sec | 4.4sec |
Feed motor | AC4.0kw(Model22/3000i) | |
Index drive system | FANUC35i-MB α12/3000i | |
Number of multi-spindle heads | 4sets/6sets | |
Size of each multi-spindle head | 500mm×600mm | 400mm×500mm |
Hydraulic tank unit | 30L(Inverter is attached) | 60L |
Multi-spindle head clamp system | Mech | |
Total weight | 8,000Kg | 11,000Kg |
There may be a change on specification for improvement without notice. Please note that.